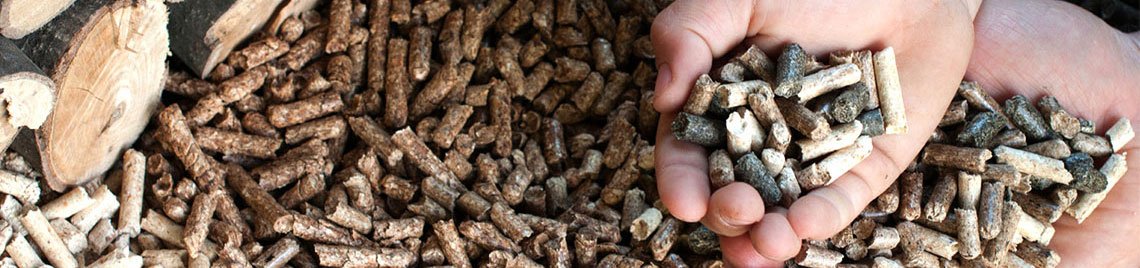
Common problems and countermeasures of biomass ring die pellet machines
Biomass energy refers to the organism produced by photosynthesis utilizes atmosphere, water and soil, mainly contains kinds of animals, plant and microorganism. Recent years, biomass energy has received the attention of many countries because of the advantages of wide range, renewable and low pollution.
In China, the government pays more attention to the biomass energy and we have achieved multiple excellent results, such as biomass pellets as fuels, biomass hydrogen production, biomass liquid fuel and so on. Since biomass energy has the support of government, it has the bright prospect. Among the biomass energy, biomass pellets made by pellet machines are popular and can be developed widely. Generally speaking, pellet machines contains flat die pellet machine and ring die pellet machine according to the structural style, with the advantages of high production capacity, good adaptability to material, stable working condition and continuous production. Here let’s talk about ring die pellet machines.
Working principle of ring die pellet machines
Ring die pellet machines can process the agricultural and forestry wastes into pellets, the mainly process is crushing, drying, pelletizing, cooling and packaging, among which pelletizing is finished by ring die pellet machines.
When working, the motor drives the ring die to rotate clockwise at a certain speed. The material enters the pellet machine chamber under the action of its own gravity and the centrifugal force of the ring die, and the material begins to be grabbed into the working area. The pressure roller rotates in the same direction as the ring die under the action of the friction force in the working area. When the extrusion pressure increases enough to overcome the friction between the material and the inner wall of the ring die hole, the material with certain bonding force and density is squeezed into the ring die hole. And the temperature is getting higher, and the lignin in the material is about the same. Because of the continuous rotation of the die roll, the material is continuously squeezed into the ring die hole, and the material that has been formed in the ring die hole is continuously extruded out of the ring die hole. Under the action of its own gravity and external cutter, the material is cut off, and the material is broken into a granular fuel of a certain length, which falls from the exit of the die hole.
Problems existing in pelletizing of biomass ring die pellet machines
Serious wear
When the biomass ring die pellet machine is working, the pressure roller squeezes the material into the ring die hole through friction and extrusion force. Up to now, the wear problem of the key parts of the biomass ring die pellet machine used in our country is more serious. Especially, the wear of roller and ring die is the most serious.
Energy consumption is large
To reduce the energy consumption of biomass ring die pellet machine has become one of the hot researches at home and abroad. For the biomass fuel processing system, energy consumption is an important performance index, energy consumption refers to the ratio of briquette production quality briquette in unit time, the amount of energy consumed and the time of production. The energy consumption of compression molding mainly includes three parts: the raw material feed consumed energy; consumption of material and forming components of wall friction energy; overcome the material elastic deformation energy required.
There are many factors that affect the energy consumption of biomass ring die pellet machine, such as particle size, moisture content, additive and other physical and chemical properties, as well as ring die size, die hole size, ring mold speed and other related parameters of the machine.
Analysis of countermeasures for ring die pellet machine
From the point of view of equipment improvement, in order to avoid the fast friction loss of biomass ring die pellet machine caused by high pressure and high temperature and the abnormal operation caused by excessive temperature, it is necessary to further improve the quality of raw materials. Based on the present situation, water cooling and temperature control technology is used to further control the operating temperature of the physical biomass ring die pellet machine. The structure of biomass ring die pellet machine is optimized, which not only improves the operation continuity of biomass pellet machine, but also reduces the biomass briquetting mechanism. The wear of the key parts, at the same time, the technology has made the corresponding structure optimization design to the lubrication system of the biomass ring die pellet machine and its mould, which ensures the equipment can always run in an optimum temperature environment, and improves the working environment. It effectively eliminates the accidental fault of the equipment, reduces the wear rate of the extrusion system and die of the equipment, and enables the equipment to work stably for a long time, which opens up another important way for the technical development of the straw forming equipment.
From the angle of forming principle, in order to abandon the forming method of traditional biomass ring molding equipment, in which the material is pressed into the ring die forming hole by pressing the outer surface of the roller, the principle of plunger meshing can be adopted, which distributes a series of plunges evenly on the outer surface of the pressing roll. The biomass material entering the ring die forming hole is extruded effectively, which avoids the strong extrusion and friction of the biomass material outside the pressure roll surface, thus reducing the energy consumption in the non-effective compression molding. At the same time, the wear of the ring die forming hole is reduced, and the service life is increased.
Conclusion
Although the domestic biomass ring mold technology has made great progress in recent years, compared with the developed countries, the most prominent problems are wear and energy consumption. Reducing energy consumption of biomass ring die pellet machine will be the focus of future research. It is also an urgent problem to be solved. To fundamentally improve the production of biomass ring die pellet machines and the quality of molding particles, and to reduce the energy consumption and wear of the molding, we also need to improve the details by changing the shape of the hole in the ring die, the clearance of the die rolls, and so on.